Yes, an AC/DC TIG welder is necessary for professional welding. It provides versatility and precision.
Recommended Best TIG Welder for Aluminium 2025
Recommendation | Product |
Best Overall | YESWELDER MIG-250 PRO Aluminum MIG Welder |
Popular Choice | TOOLIOM Aluminum MIG Welder |
Best Value | LOTOS MIG225SP MIG Welder |
Best Budget | AZZUNO Aluminum MIG Welder |
Another Excellent Pick | HITBOX TIG Welder AC/DC Aluminum Welding Machine |
Both are crucial in professional settings. Welders often face different materials and projects. An AC/DC TIG welder offers flexibility. It can handle aluminum, steel, and more. This versatility ensures you can tackle any job. The precision of TIG welding is also unmatched.
It allows for clean, high-quality welds. Professionals need reliable tools. An AC/DC TIG welder meets this need. It ensures you can deliver top-notch results. Investing in one can elevate your work. It makes complex tasks easier. For professional welders, this tool is essential.
Introduction To Tig Welding
Deciding if an AC/DC TIG welder is necessary for professional welding depends on the materials used. AC is ideal for aluminum, while DC suits steel. Both options offer versatility and precision for various projects.
TIG welding stands for Tungsten Inert Gas welding. It is a precise welding method. It uses a tungsten electrode to produce the weld. This technique is popular among professional welders. It is known for producing high-quality and clean welds.
Basics Of Tig Welding
TIG welding requires a steady hand. The welder uses a non-consumable tungsten electrode. An inert gas, usually argon, shields the weld area. This process prevents contamination. It can be used with or without filler material. This method allows for great control over the weld.
Common Applications
TIG welding is used in many industries. It is ideal for welding thin materials. Aerospace uses TIG welding for precision tasks. It is also common in automotive repair. Artists and sculptors use TIG welding for detailed metalwork. This method is perfect for stainless steel and aluminum projects.
Understanding Ac/dc Tig Welders
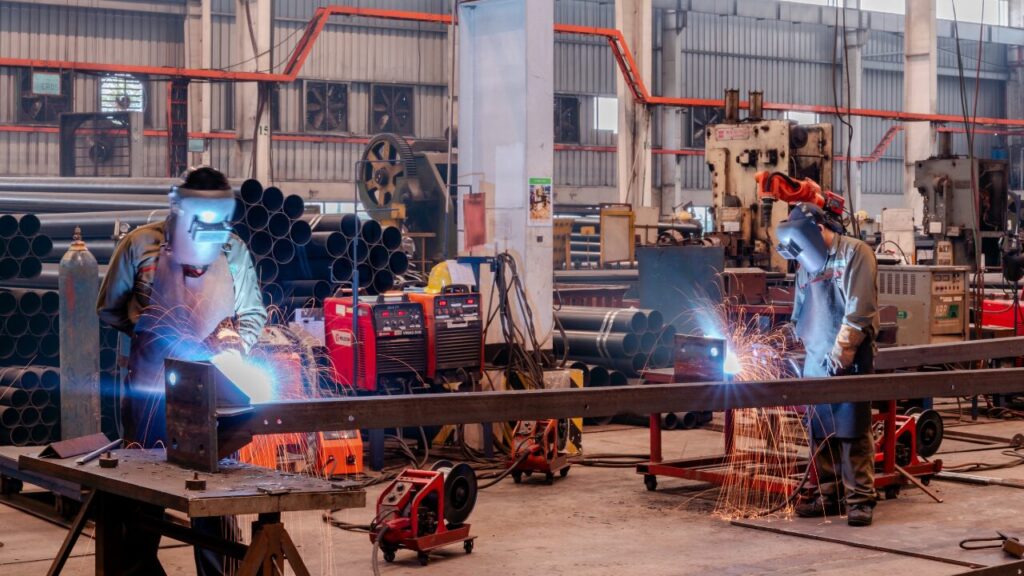
When it comes to professional welding, the choice of equipment can make a significant difference in the quality of your work. One critical decision is whether to invest in an AC/DC TIG welder. Understanding the benefits and functionalities of AC/DC TIG welders is essential for making an informed decision. This section will delve into what makes these welders unique and why they could be necessary for your welding projects.
Ac Vs Dc Explained
AC and DC refer to the type of current used in welding. Alternating Current (AC) switches direction periodically, while Direct Current (DC) flows in one direction. Each type has specific applications:
- AC Welding: Ideal for welding aluminum and magnesium. It cleans the oxidized layer on aluminum, leading to a cleaner weld.
- DC Welding: Suitable for welding steel, stainless steel, and other metals. It provides stable arcs and deeper penetration.
Understanding the differences between AC and DC welding can help you choose the right welder for your projects. If you frequently work with aluminum, an AC/DC TIG welder is a worthwhile investment.
Key Features
AC/DC TIG welders come with a variety of features that enhance their functionality and ease of use:
- High-Frequency Start: Provides a non-contact arc start, which is crucial for a clean weld.
- Pulse Control: Allows you to control the heat input, reducing warping and improving weld quality.
- Adjustable AC Frequency: Gives you more control over the arc cleaning action, especially useful for aluminum welding.
- Dual Voltage Capability: Enables you to use the welder with different power supplies, increasing flexibility.
These features make AC/DC TIG welders versatile tools in a welder’s arsenal. But, is it necessary for your professional work?
Consider your projects: Do you often work with a variety of metals? Are high-quality, clean welds essential for your reputation and customer satisfaction? If your answer is yes, then investing in an AC/DC TIG welder can significantly enhance your capabilities and output.
Moreover, the ease of switching between AC and DC modes without changing machines saves time and increases efficiency. This is a game-changer for professional welders who need to meet tight deadlines and maintain high standards.
If you’re serious about welding, the versatility and advanced features of an AC/DC TIG welder could be the key to elevating your craft. Are you ready to take your welding to the next level?
Benefits Of Ac/dc Tig Welders
AC/DC TIG welders offer flexibility for professional welders. They handle various metals like aluminum and steel. This makes them essential for high-quality welding tasks.
When it comes to professional welding, the choice of equipment can significantly impact the quality of your work. An AC/DC TIG welder stands out as a versatile and precise tool, offering numerous benefits that can enhance your welding projects. Let’s explore these advantages under specific aspects.
###
Versatility In Materials
One of the standout benefits of AC/DC TIG welders is their ability to handle a wide range of materials. Whether you’re working with aluminum, stainless steel, or even exotic metals like titanium, an AC/DC TIG welder can manage it.
Have you ever faced a project where you’re required to switch between different types of metals? It can be quite a hassle if you don’t have the right equipment. With an AC/DC TIG welder, this is no longer a problem. You can seamlessly switch from welding aluminum using AC to steel with DC, all with the same machine.
This versatility is not just about convenience. It translates to cost savings and efficiency. You won’t need multiple welders for different materials, saving both space and money.
###
Precision And Control
Another significant advantage of using an AC/DC TIG welder is the precision it offers. TIG welding is known for its ability to create clean and precise welds, but an AC/DC machine takes it a step further.
Imagine you’re working on a delicate project, perhaps an intricate automotive part or a custom-made bicycle frame. The ability to precisely control the heat input and welding speed can make a world of difference. An AC/DC TIG welder allows you to fine-tune these parameters with ease.
Moreover, the control you have over the welding arc is unparalleled. You can achieve those perfect, consistent beads that not only look good but also ensure structural integrity.
Have you ever struggled with keeping a weld bead uniform? With the control offered by an AC/DC TIG welder, that becomes much easier. You can adjust settings on the fly, ensuring that each weld is just as you want it.
Using an AC/DC TIG welder, you can achieve a level of precision that is hard to match with other types of welding equipment. This makes it an invaluable tool for professionals who demand the highest quality in their work.
In conclusion, the versatility and precision of AC/DC TIG welders make them an essential tool for professional welders. Whether you’re dealing with various materials or require exact control over your welds, this equipment can meet your needs effectively. So, is an AC/DC TIG welder necessary for professional welding? If you value versatility and precision, the answer is a resounding yes.
Comparing Ac And Dc Welding
Choosing between AC and DC welding can be challenging for professionals. Each type offers unique benefits and disadvantages. Understanding their differences helps in making an informed decision. This section covers performance differences and best use cases for AC and DC welding.
Performance Differences
AC welding provides a balanced arc, which is ideal for working with aluminum. It helps in removing the oxide layer. This results in a clean weld. DC welding, on the other hand, offers a stable and smooth arc. It is suitable for most metals, including steel and stainless steel. DC welding allows for better penetration and a more consistent weld. This makes it a preferred choice for many professionals.
Best Use Cases
AC welding is best for aluminum and magnesium. These metals have a tough oxide layer. AC welding breaks through this layer effectively. For thicker materials and general fabrication, DC welding is the go-to option. It is also ideal for working with steel, stainless steel, and other common metals. DC welding is often used in construction, automotive, and manufacturing industries.
When Ac/dc Tig Welders Are Essential
In the world of professional welding, the type of equipment you use can significantly impact the quality of your work. One of the most debated pieces of equipment is the AC/DC TIG welder. Let’s delve into the scenarios where this tool becomes not just useful but essential.
Professional Settings
If you work in a professional welding shop, you’ve probably encountered a variety of metals, each requiring a specific welding technique. AC/DC TIG welders shine in these settings. I remember working on a project that involved both aluminum and stainless steel. The versatility of having an AC/DC TIG welder allowed me to switch between metals seamlessly. You can’t afford to be switching machines or techniques mid-project in a professional setting. This flexibility can save you both time and money, making your workflow more efficient.
Complex Projects
Complex projects often require precision and the ability to work with different materials. I was once tasked with fabricating a custom bike frame, which involved both aluminum and chromoly steel. An AC/DC TIG welder was indispensable. The AC setting was perfect for the aluminum parts, providing smooth and clean welds. Meanwhile, the DC setting allowed me to handle the steel components with the precision required for such a project. Can you imagine trying to complete such intricate work with a less versatile machine?
AC/DC TIG welders offer the control needed for complex welds. You get to manage the heat input and ensure that the weld pool is just right. This kind of precision is crucial when working on detailed projects where a single mistake can ruin hours of work.
Have you ever found yourself in a situation where your current equipment just doesn’t cut it? Upgrading to an AC/DC TIG welder might be the solution. These welders are not just tools; they are investments in quality and efficiency.
So, the next time you’re considering what equipment to add to your welding arsenal, think about the demands of your projects. An AC/DC TIG welder could be the game-changer you need.
Cost Considerations
Considering an Ac/Dc TIG welder’s cost is crucial for professional welders. These machines offer versatility but can be expensive. Evaluate your budget and welding needs before investing.
When considering whether an Ac/Dc Tig Welder is necessary for professional welding, one crucial factor to evaluate is the cost. Understanding the financial implications can help you make an informed decision that aligns with your needs and budget. Let’s delve into the cost considerations associated with these versatile welding machines.
Initial Investment
The initial investment in an Ac/Dc Tig Welder can be significant. Prices for these machines vary widely, depending on the brand, features, and power capabilities. Entry-level models might start around $1,000, but high-end professional-grade welders can easily exceed $3,000.
This upfront cost might seem daunting. However, consider the quality and versatility an Ac/Dc Tig Welder brings. You’re not just buying a tool; you’re investing in a reliable piece of equipment that can handle a variety of welding tasks.
When I first purchased an Ac/Dc Tig Welder, I was hesitant about the price. But the machine’s performance in diverse projects—from stainless steel to aluminum—proved invaluable. The initial expense soon felt justified as my productivity and project quality improved.
Long-term Value
While the initial cost is a significant factor, the long-term value of an Ac/Dc Tig Welder is equally important. These machines are built to last, offering durability and consistent performance over many years.
Consider the potential savings in repair and replacement costs. A high-quality welder reduces downtime and increases efficiency, which translates to more completed projects and satisfied clients.
Additionally, the versatility of an Ac/Dc Tig Welder means you won’t need to invest in multiple machines for different materials. This flexibility can save you money and space in your workshop.
Think about the potential return on investment. How much more work could you accomplish with a reliable and versatile welder? How much would you save on maintenance and replacements?
Ultimately, the decision to invest in an Ac/Dc Tig Welder should balance the initial cost with the long-term benefits. By carefully considering these factors, you can make a choice that supports your professional welding endeavors for years to come.
Alternatives To Ac/dc Tig Welders
Is an AC/DC TIG welder the only option for professional welding? Not necessarily. Several alternatives can meet your welding needs. These alternatives offer different features and benefits. Let’s explore these options.
Other Welding Types
MIG welding is a popular alternative. It stands for Metal Inert Gas welding. This method is fast and efficient. It works well on thin and thick metals.
Stick welding, also known as Shielded Metal Arc Welding (SMAW), is another option. It’s versatile and works in various conditions. It’s also cost-effective.
Flux-Cored Arc Welding (FCAW) is similar to MIG welding. It uses a flux-filled wire. This process is ideal for outdoor work. It handles dirty or rusty metals well.
Pros And Cons
MIG welding’s main advantage is speed. It’s user-friendly and produces clean welds. But it requires a shielding gas. This gas can be a drawback in windy conditions.
Stick welding is versatile and affordable. It works in any position and with various metals. But it can be messy. It also requires more skill to master.
FCAW is great for outdoor work. It doesn’t need a shielding gas. It handles dirty metals well. But it produces more spatter. It also requires more cleanup.
Choosing The Right Tig Welder
Choosing the right TIG welder is crucial for achieving top-quality welds. The welder you select can make your work easier and more efficient. There are a few factors to consider when making your choice. Let’s break down these factors to help you decide.
Assessing Your Needs
First, consider the type of projects you handle. Are you working on light materials or heavy-duty welding? Different welders are designed for different tasks. Think about the thickness of the materials you weld. Also, consider the metals you work with most often. Aluminum and stainless steel may require different settings. Knowing your needs helps narrow down your choices.
Top Brands And Models
Several brands are known for their high-quality TIG welders. Miller Electric is a popular choice among professionals. Their machines offer durability and precision. Lincoln Electric is another trusted brand. They provide reliable and user-friendly welders. ESAB is known for its innovative features. Their models often include advanced technology. Researching these top brands can help you find the right welder for your needs.
Frequently Asked Questions
Do I Need Ac/dc Tig?
You need AC/DC TIG for welding both aluminum and steel. AC is used for aluminum, while DC is for steel.
What Are The Disadvantages Of Ac Dc Welder?
AC DC welders can be more expensive and complex. They require more maintenance and can be less efficient for certain tasks.
Can You Tig Weld With A Dc Welder?
Yes, you can TIG weld with a DC welder. DC welding is suitable for stainless steel, carbon steel, and copper.
Can I Weld Aluminum With A Dc Tig Welder?
Yes, you can weld aluminum with a DC TIG welder, but it’s challenging. DC can cause contamination and poor weld quality. Using AC is recommended for better results.
Conclusion
Choosing an Ac/Dc Tig welder depends on your welding needs. For professionals, it offers versatility and precision. It handles various metals effectively. Beginners may find it complex but rewarding with practice. Consider your projects and budget. Quality welds often justify the investment.
Research and compare models. Consult experts if unsure. A suitable welder enhances your craft and efficiency. So, assess your requirements carefully. A well-informed choice supports your welding success.